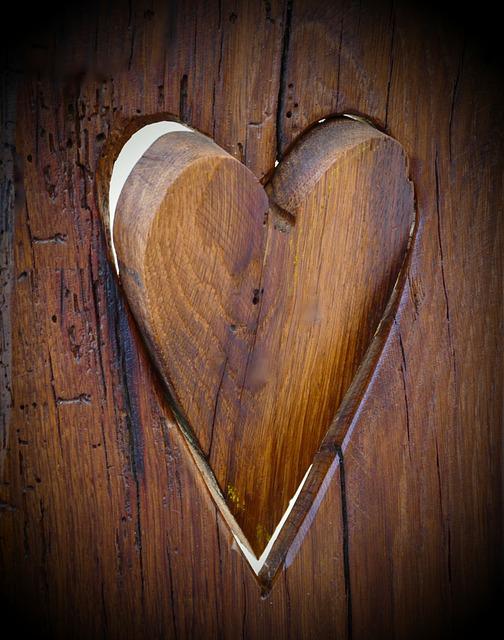
This is the place to learn how to carve wood-carved caricatures. Here you'll learn about the designs, techniques, and safety. You can make a simple caricature into an artful masterpiece. You don't have to know where to begin if you aren't sure how to get started. Here are some tips for making your caricature stand out. There are also classes offered by caricaturists.
Techniques
Wood carving caricatures is a rare form of sculpture. They're amusing and can tell a story without words. Caricature refers to a distorted representation of a human being. Dave Stetson and other wood carving carvers adhere to strict rules to ensure realistic results. This article will give you tips and the basics of carving caricatures.
First, it is important to focus on the technique for carving an astronaut. The two most delicate tools for carving an astronaut are the whittling or spoon knives. You can also use templates to help you make your work easier while carving the astronaut. A tutorial will give you step-by-step instructions for how to complete your caricature. If you're working on a budget, you might want to look into buying a tutorial for this specific subject.
Designs
There are many options for creating wood-carved caricatures. Using a pattern is a great way to start. You can also purchase a cutout of cardboard and use the same patterns to create different caricatures. You can also refer to a tutorial for caricature carving. This article will help you learn about the best techniques and designs for carving a caricature.
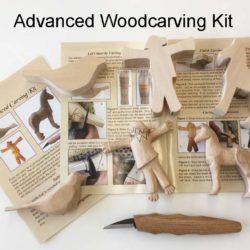
The first caricature that Fred made was called 'Aristocrats of the Roads'. It depicted two men who wandered. It was carved from Honduras Mahogany. Fred entered it into competitions and won several awards. It was also featured on the Chipping Away Catalog. Fred created a second Luciano Pavarotti caricature in 2009. He won a Second Runner up Award at a national woodcarving convention.
Eyes
The first thing to remember when carving caricatures of people is to make sure the eyes look realistic. There is nothing wrong in having realistic looking eyes. However, viewers may not be satisfied with a caricature lacking the right amount detail. You can make sure your eyes are perfectly symmetrical by taking a photo of an existing carving. Follow the steps in the photo.
Next, the shape and size of the eyes must be determined. Some carvers have the same eye shape. Others use different shapes to create more believable eyes. Stop cuts can be used to make your eyes symmetrical. Lastly, you will need to carve the pupil and the iris. Now you are ready to start carving the caricature.
Safety
Wood carving caricatures can be unique in their design. They tell stories without the use of words. Artists who create them take great pride in their accuracy. Caricatures are usually depictions that exaggerate people or things to convey an impression. Dave Stetson, wood carving carver has established stringent rules for carvers safety and quality.
First, clean the wood thoroughly and remove pencil marks. The surface can be cleaned with water and dish soap. The 60-degree V-shaped tools can be used to carve the neck. A 60-degree V shape tool is useful for carving, as it cuts wood easily. Ramelson's 60-degree V-shaped Carving Tool is an excellent choice. It is very sharp and easy-to-use.
Materials
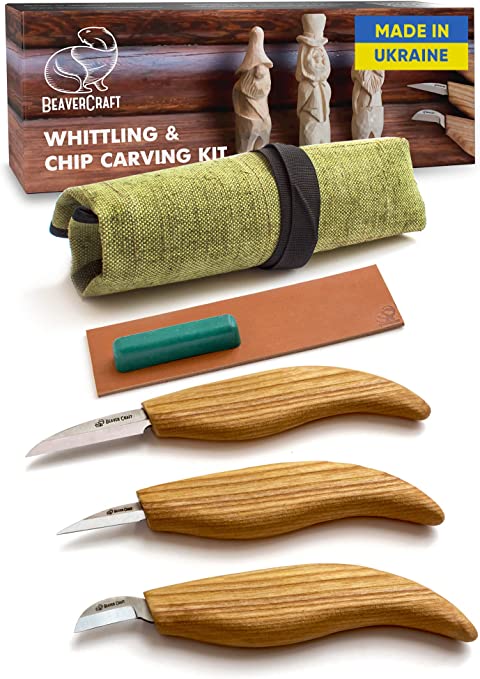
The wire and wood caricatures are a fun, challenging way to carve animal figures. Even though animal caricatures might not be as complex as human caricatures but they are still entertaining and can tell a story with no words. Caricatures can be exaggerated to evoke realism. For beginners, carving caricatures can be difficult. However, for more skilled carvers, there are many materials available.
A wood board and chisels are the two main materials that you need for carving. A hammer is also necessary. Acrylic white paint can be used as the base layer. It is available at craft stores. The second layer can be added once the base layer is completed. This layer will consist of a golden brown paint and a few drops of burnt sienna (Academy). Use 2 drops of sunkissed pearl for the face.
FAQ
Is it possible to open my own woodworking shop?
It's not easy to start your own woodworking business. You will need to adhere to many legal requirements. It doesn't mean that you have to go through the entire process of starting a business. Many people prefer to join existing companies. This allows you to join existing businesses and pay only membership fees.
How much should a skilled woodworker earn per hour?
The hourly rate paid to a professional woodworker is dependent on many factors. These include skill level, availability, and location.
A skilled woodworker can expect an hourly rate of $20-50.
A less experienced woodworker may charge as little as $10 an hour.
You can learn how to woodwork.
It is best to do it yourself. Woodworking is an art form that requires patience, practice, skill, and experience. Any craft requires patience to master.
The best way to learn how to do something is actually to do it. Start small, and work your way up from there.
What's the difference between a hobbyist and a professional woodworker?
Hobbyists enjoy making things out of wood, whereas professionals focus more on the quality of their work. Hobbyists are proud of their creations and will often share them with family members and friends. Professionals will spend hours researching designs and then begin to create a project. They will pay attention to every detail, from selecting the best materials to finishing the project perfectly.
Which wooden items are very popular?
The most successful wooden items are made from sustainable wood.
The most popular types of wood for furniture include oak, maple, cherry, mahogany, walnut, and teak.
These woods are very strong, but they also have beautiful grain patterns and colors. If they are well cared for, they can last many years.
Wooden furniture should always be painted first to protect against moisture damage. This covers all surfaces, drawers included, as well as doors and handles.
A paint that resists water is the best choice to ensure that furniture lasts a long time.
A high-quality oil-based primer should be used, followed by two coats with top coat. It is possible to apply multiple coats depending on how heavy the wear.
Spray cans or aerosol paints should be avoided. These products are contaminated with solvents, which evaporate rapidly and can leave behind toxic fumes.
Statistics
- In 2014, there were just over 237,000 jobs for all woodworkers, with other wood product manufacturing employing 23 percent; wood kitchen cabinets and countertop manufacturing employing 21 percent. (theartcareerproject.com)
- Most woodworkers agree that lumber moisture needs to be under 10% for building furniture. (woodandshop.com)
- If your lumber isn't as dry as you would like when you purchase it (over 22% in Glen Huey's opinion…probably over 10-15% in my opinion), then it's a good idea to let it acclimate to your workshop for a couple of weeks. (woodandshop.com)
- Woodworkers on the lower end of that spectrum, the bottom 10% to be exact, make roughly $24,000 a year, while the top 10% makes $108,000. (zippia.com)
External Links
How To
How to join hardwood without using nails
Woodworking is a favorite hobby. You can make useful items from wood with your hands, which is both relaxing and fun. However, there are times when you want to join two pieces of wood together without having to use nails. This article will show you how to do it to make your woodwork projects look great.
Before joining the pieces of wood together, you will need to first trim any edges. Do not leave any sharp corners as they could cause problems down in the future. Once you have done that, you can begin gluing your boards together.
If you are working with hardwood, only one side should be glue. You should glue both sides if you are working with softwoods such as pine and cedar. Press the boards down until the glue is fully incorporated. Before moving onto the next step, make sure the glue has dried completely.
After you have glued the boards together, drill holes in the joints where you intend to place screws. These holes will differ depending on the type and size of screw you are using. If you plan to use a 1/2 inch wood screw, drill a hole at least 3/4 inches in depth.
After drilling your holes, drive the screws into the board's backside. You should be careful not to touch the board's front surface. This could cause damage. When driving the screws, try to avoid hitting the ends of the screws too much. This will prevent splitting the wood's end grain.
Once your project is complete, it's time to protect it against the elements. You can either seal the entire piece of furniture or cover the top. Either way, you'll want to use a product that will last for years to come. Examples include oil-based varnishes and polyurethanes, shellac, lacquer and others.
These products can usually be found at any home improvement store. You should make sure you are getting the right type for the job. Some finishes are toxic and should not ever be used indoors. Always wear protective gear when handling any of these finishes.