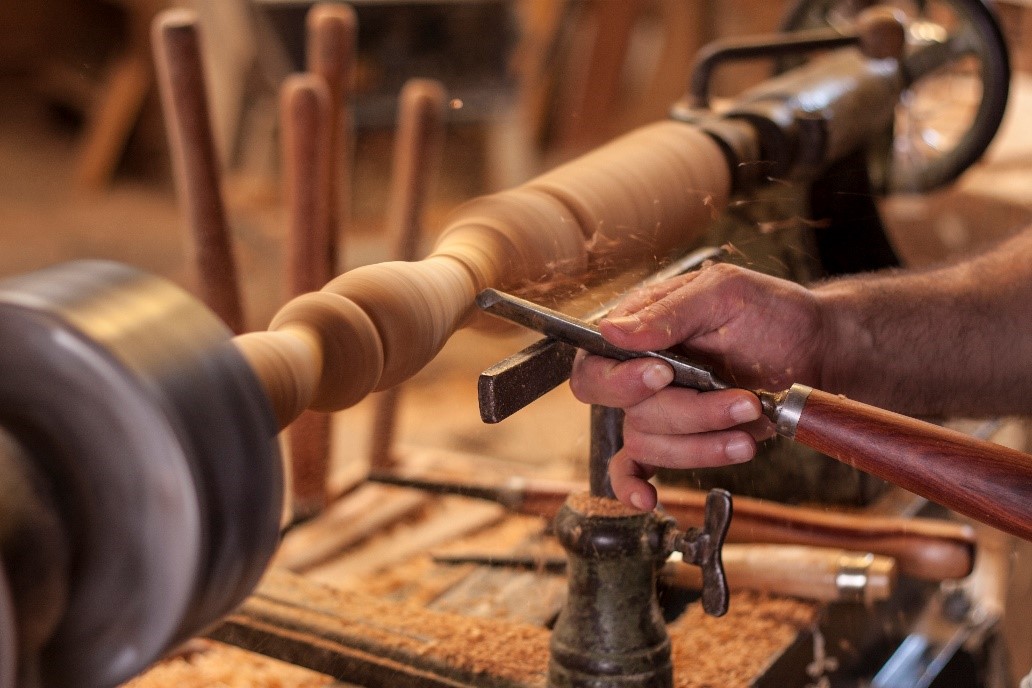
Chattahoochee Woodturners joined forces with Eagle Ranch to help build a woodturning facility on the school's campus. The American Association of Woodturners gave an Educational Opportunity Grant, as well as other donations, to help them build the facility. Local woodturners donated equipment as well as tools to help get this project off the ground. Open to all students is the woodturning class, as well as a woodshop that is accessible for adults with disabilities.
Hark woodturner
Hark first started woodturning at Harvard University's Mather Building eight years ago. He was approached by Hark after a class. Hark agreed to teach the Harvard class. After several unsuccessful attempts to teach the course in Harvard, Hark eventually found an old lathe from a basement of a neighboring house. That spring, his first Harvard class started. Students from all Harvard Houses are invited to the woodturning workshop's classes today. He also continues teaching woodturning on weekends.
Arthur and Pamela are not only teachers, but also travel to trade shows and woodworking symposiums in search of new audiences. They have hosted many world-renowned artists as guests and have met many others. Woodturning workshops featured many artists from all walks of life. The studio has also sent a Commander and Knight to the Norwegian Woodturning Cruise which is held every three-years.
Tools
Safety gear is a must-have in any woodturning studio. To protect your eyes and prevent the glares of sand from damaging your skin, you may need safety goggles or a helmet. Sharpening tools can also be an investment. You will also need safety gear. A jigsaw and lathe are essential to sharpen lathe blades.
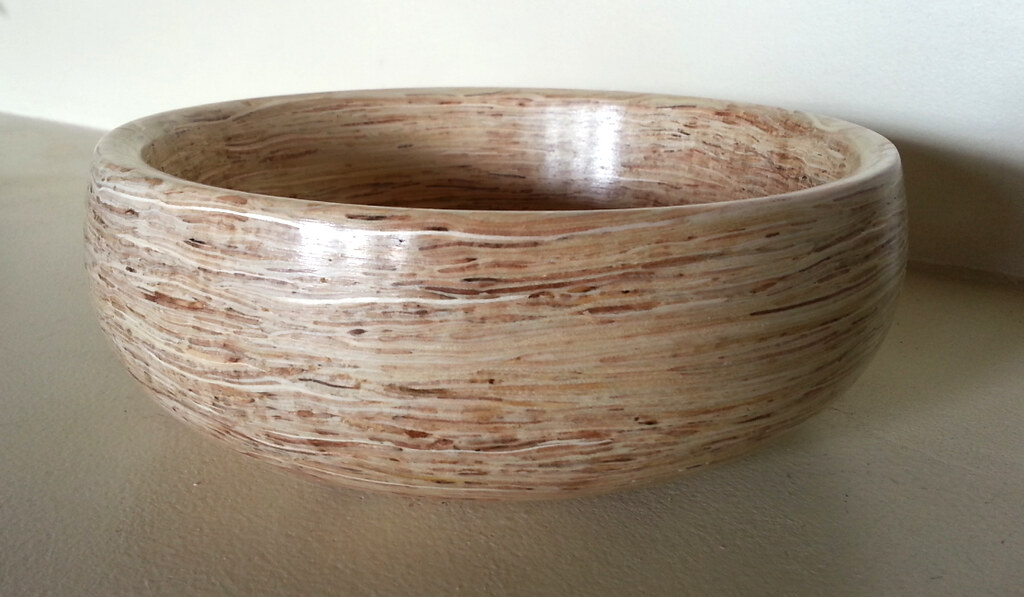
Some of the most basic tools that you'll need are the banjo, a screwdriver, and a drill. The banjo allows you to slide your turning tool along the bed of the lathe, supporting the toolrest. This allows the tool to be held in the most convenient position. Modern lathes come with a locking mechanism that locks the banjo. These tools will help you create your custom creations.
Techniques
No matter whether you're interested in hobby woodturning or are a professional, it is essential to learn the best tools and techniques for woodturning. These tools are crucial for creating functional and beautiful pieces that will be both functional and attractive. These tools are available online and at your local woodworking store. It is not an easy process to turn wood, but it is worth the time.
A woodturning course is a great way of learning the basics if you're just getting started. Workshops will teach you everything from how to choose the right tools, safety gear, and how to use them. You will also have hands-on experience with a lathe. It will be a hands-on experience to learn tools properly and to apply the techniques to your own work. You can make anything you want, depending on what skills you have.
Class size
If you're new to woodturning, and want to learn the basics, then a beginner workshop at a Durham woodturning shop may be for you. This class will teach you basic techniques, how to sharpen tools and how to use them. A variety of projects will be included as part of the class. Safety is the main focus of the instructor. Please bring your own protective equipment and a face mask.
The small class size allows you to pay attention to each student's progress. The instructors will have plenty of time to answer questions and provide individual attention. There will often be six or fewer students in a class. This allows for a more relaxed learning environment. Most of the classes are project-based. They will usually last for a few days. Private lessons can focus more on advanced techniques for those who are more skilled.
Cost
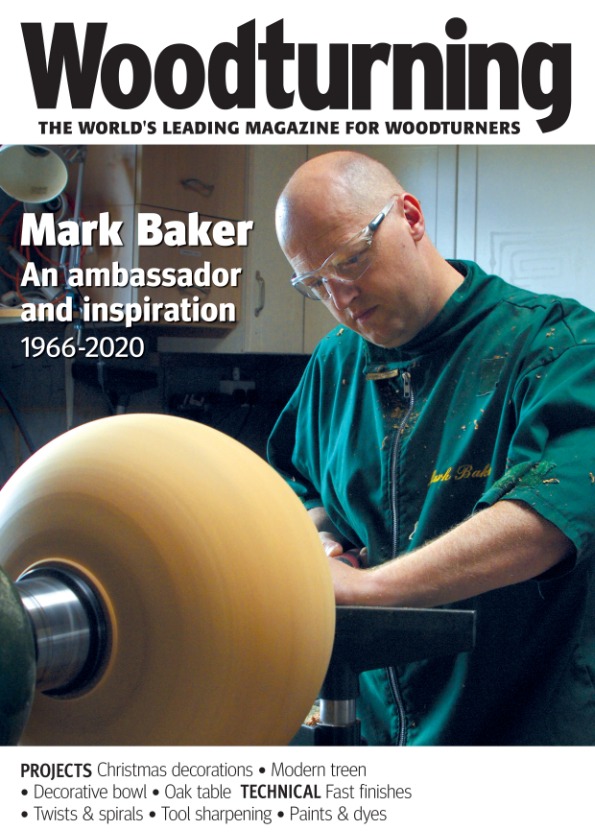
Setting up your own woodturning studio will be an expensive endeavor. It is not uncommon for equipment and supplies to cost more than a few thousand dollars. You can save money by selling your finished products at a low price. Selling your finished products can increase your profits by up to three times. While high-end pieces are a great way to promote your art and generate profits, you may also want to sell items at a lower price point. While high-end items may take longer to produce, you can always sell simple items in this price range. They can even sell out in the first day of an art show that lasts two days.
A class will help you get started in woodturning. This will include safe use of tools as well as proper sharpening. This will allow you to move on to more difficult projects and teach you more advanced tools and techniques. For Mather residents and Harvard affiliates, an introductory woodturning class costs $75. All materials and tools are included in the price. A list of nearby hotels will be included.
FAQ
What tools do I need to start as a woodworker and what should I learn?
Woodworking is an art form that requires patience and practice. It takes time and practice to master the various techniques and tools required for woodworking.
There are many woodworking tools on the current market. Some people prefer to use power tools while others prefer manual tools.
While you have the option to pick what you like, it is essential that you get the right tool for the job. A basic set of hand tools may be enough for you if your skills are not yet developed.
A router is a tool that cuts intricate shapes in wood. You can also learn how to use it. You can find these at most hardware stores.
What is the average time it takes to finish furniture?
It depends on the size and condition of the furniture. For smaller projects such as picture frames and boxes, it can take less than a day to complete. Larger projects, like desks or dining tables require several days. It takes time for the wood to be stained and sealed properly.
How can you calculate woodworking pricing?
The most important thing to remember when calculating costs for any project is to keep them as low as possible. Make sure you're getting the best prices on materials. It is important to take into consideration all factors that can impact the cost of your projects. These include time, skill and experience. You can find an estimate of the cost of different woodwork projects in our guide to common DIY tasks.
What is the hourly rate for a woodworker?
The hourly rate for a professional Woodworker will vary depending on many variables, such as experience, skill level and availability.
The hourly average rate for skilled woodworkers runs between $20-$50.
A less skilled woodworker might charge as low as $10 per hour.
Where can I purchase woodworking supplies
There are many places where you will find everything that you need. You can visit your local hardware stores, or you can look online at sites like Amazon.com.
You can also check garage sales and flea markets for old furniture and other materials you can reuse.
How often should I get new supplies?
You may have to replace certain tools. Sharpening hand tools is a must. If you are using power tools, you will need to purchase replacement parts regularly. Try spreading your purchases over a few months so you don't buy too many at once.
What kinds of woods are good for making furniture?
Woods are classified based on their hardness. Softwoods can be pine, fir or cedar. They're often used for outdoor furniture because they don't rot easily. These hardwoods include maple, mahogany and teak. Because they can't weather outside, they're usually used indoors.
Statistics
- If your lumber isn't as dry as you would like when you purchase it (over 22% in Glen Huey's opinion…probably over 10-15% in my opinion), then it's a good idea to let it acclimate to your workshop for a couple of weeks. (woodandshop.com)
- Overall employment of woodworkers is projected to grow 8 percent from 2020 to 2030, about as fast as the average for all occupations. (bls.gov)
- Woodworkers on the lower end of that spectrum, the bottom 10% to be exact, make roughly $24,000 a year, while the top 10% makes $108,000. (zippia.com)
- Average lumber prices rose about 600 percent between April 2020 and May 2021. (familyhandyman.com)
External Links
How To
How to make wood joints
This tutorial will demonstrate how to join two pieces together of wood. We will use the "pockethole joint," which means that we drill holes in the wooden pieces and then glue them together. If your wood is straight and flat, this method will work well. You might consider dowel joinery if your wood isn’t straight or flat. Here are the steps
-
Drill Pocket Hole Joints. Start by measuring and marking the spot where the pocket hole joint will be placed. With a handheld drill machine or jig saw, drill 3/4-inch deep holes in the ends of each piece.
-
Sand Smooth. You can sand the edges of the wood to ensure that it doesn't split.
-
Glue together. Apply glue to both the ends of the wood. Allow the wood to rest for five minutes before clamping it together.
-
Secure the pieces together. After the glue has dried properly, clamp the pieces together to make sure they are flush.
-
Trim Joinery. After the glue dries completely, trim off any excess wood around the joint.
You should leave enough space between the pieces to allow you to turn them inside-out.