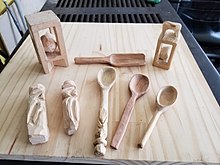
Woodcarving, or whittling, is one of two techniques. Both of these techniques involve removing wood from a larger piece of wood and changing it into a new shape. You can create anything from a spoon for the kitchen to a 10 foot carving, but the most important difference is that both require the removal of wood material from the original piece. Wood carving, unlike whittling that requires clamping and gluing as well as joinery, does not require any of these methods.
Woods to carve
There are many different types of wood that can be used to carve. You can choose from fresh, green, moist or rotten woods. Because of their ease in carving, ensure that they have straight grain and minimal knots. For carving, wood with large knots or side branches is not recommended. Ask park wardens and tree doctors for assistance in finding the best wood. They will be able to point you in the right direction.
Pine, which can be found easily in the US is one of most straightforward woods to carve. Although it is soft and has knots, it holds its details well. Pine will last long if cared for properly. In Norway, for example, the load-bearing orepine stave churches that have survived over eight hundred years have been preserved. This is a great choice if you're just starting out.
Use of tools
Before you can begin wood carving, draw your design on the wood. To cut straight lines, you can use your hand saw or a drill to make intricate details. A gouge is great for rough shaping, as it can quickly remove large quantities of material. The gouge also features an abrasive edge, which is great for smoothing out rough areas.
There are many types of knives. For finer detail work, bench knives may be used. These knives can penetrate the wood and can be used for detail work to remove larger pieces. For cutting through thicker timber, a chisel works well. However, bench knives can also be used for delicate cuts. Although chip carving and whittling are great options for beginners, having the right tools is crucial to your success.
Techniques
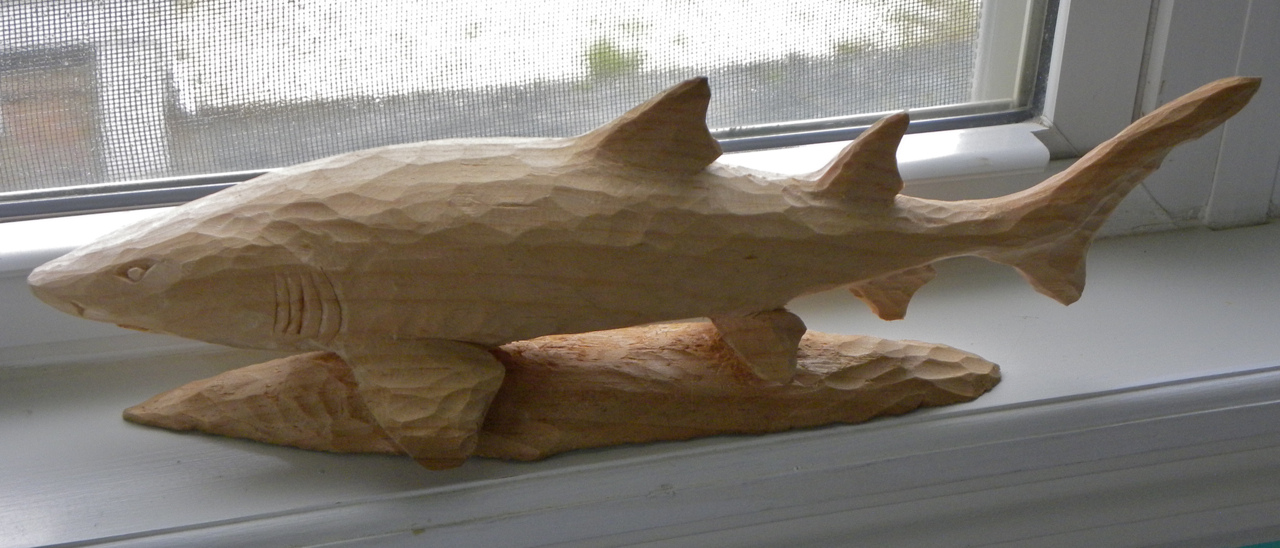
Sharp knives are necessary for precise, controlled cuts that are vital to good whittling or wood carving. A dull knife will cause frustration, blisters, or tired hands. A sharp blade also makes the process meditative and safe. Whittling enthusiasts are able to sit and think deeply and breathe rhythmically while carving intricate designs and details with the sharp knife.
There will be mistakes, just like any craft. But, mistakes are part of the process. Your first creations could be unsymmetrical, cut in the grain, split, or any other mishap. You may be overly eager to carve a nose and end up with a piece without a nose at all. To improve your skills, accept these mistakes. Wood carving is an enjoyable hobby that can encourage you to try new designs.
Whittling is one of the most common wood-carving methods. This is the oldest type of wood-carving and uses either a straight or pocket knife. Softwoods are easier to carve than hardwoods. As a result, whittling displays knife marks. The wood carvings require no sanding.
Getting started
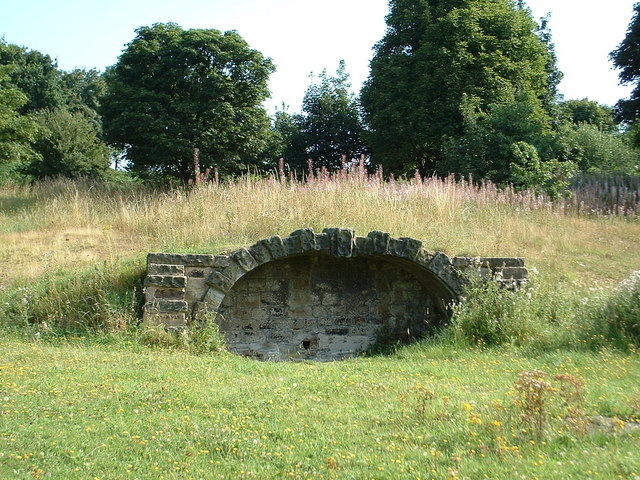
You must choose a piece to get started with wood carving. While you can use a wide variety of wood types, it is recommended that beginners start with basswood. Avoid knots and holes. It's easier to carve smooth branches. You can buy beginner-level wooden items at craft stores. Learn more about wood carving by reading the following tips.
Use the right tool. Sharpening and durability are important features of the whittling tool. For the first few cuts, use a high-quality knife. A sharp blade ensures better cuts. A dull blade can cause the blade to look off the wood and point toward the hand. However, it can also cut human flesh. When carving, these are the most important tips. This will make your carving experience much simpler. Continue reading for more information about wood carving, whittling and other related arts.
FAQ
How can you calculate woodworking pricing?
Remember to keep costs as low as you can when calculating project costs. You should always try to make sure that you are getting the best deal on materials. It is also important to consider the costs of other factors, such time, skill, and experience. Check out our guide on the average cost of common DIY projects to get an idea of how much you can spend on woodwork projects.
What is the difference in a hobbyist and professional woodworker?
Hobbyists like making things with wood. Professionals focus more on quality. Hobbyists take great pride in their creations, and share them with family and friends. Professionals will spend hours looking at designs before they start to build a project. They will meticulously plan every detail of their work from choosing the right materials to finishing it.
What material would your recommendation be to learn woodworking?
Start with softwoods such as pine and poplar. These two are the easiest to master, then you can transition to hardwood.
Is it possible to open my own woodworking shop?
It is difficult to start your own woodworking company. There are many regulations and legal requirements that you will need to comply with. This doesn't necessarily mean that you should go through all the work of setting up a company. Many people decide to join established businesses. This way, you only need to pay membership fees and taxes.
Statistics
- Woodworkers on the lower end of that spectrum, the bottom 10% to be exact, make roughly $24,000 a year, while the top 10% makes $108,000. (zippia.com)
- Overall employment of woodworkers is projected to grow 8 percent from 2020 to 2030, about as fast as the average for all occupations. (bls.gov)
- The U.S. Bureau of Labor Statistics (BLS) estimates that the number of jobs for woodworkers will decline by 4% between 2019 and 2029. (indeed.com)
- In 2014, there were just over 237,000 jobs for all woodworkers, with other wood product manufacturing employing 23 percent; wood kitchen cabinets and countertop manufacturing employing 21 percent. (theartcareerproject.com)
External Links
How To
How to stain wood
Staining wood is the process of applying chemicals to the wood's exterior, which alters its color. This chemical reaction causes the wood color to change from white and brownish red. While oak is the most widely used type of wood for staining purposes, other types of wood are also available.
You can apply wood stains in many different ways. One method involves mixing the stain and a solvent and then spraying it on the wood. Some methods involve a mixture of water and dye that is applied directly to the wood. The stain can be mixed with paints and varnishes to become part of the final coating.
Preparing the surface for staining wood is the first step. To apply the stain, clean the wood completely. Sanding the wood removes scratches and imperfections. You must then decide on the type of stain that you wish to use. There are two types of stains that can be used: penetrating and non-penetrating. Penetrating colors penetrate deeper into wood than those that are non-penetrating. This makes them more suitable for darker colors, such as mahogany. Non-penetrating stains work best with light colors like maple.
After deciding on the type of stain, you want to apply, prepare your tools. Paintbrushes are great for applying stain because they allow you to evenly spread the liquid across the surface. It is a good idea to have rags on hand in case you need them to clean up any stains that may remain after you have finished painting. You should have enough containers to store the various components of the stain mixture if you intend to mix it yourself.
Once you have prepared all your materials, it is time to clean the areas where you will stain the wood. Clean the area with soap and warm water to get rid of dirt and grime. Use a dampened rag and clean water to wipe the furniture. You should remove any debris, especially if your plan is to stain darker wood.
Apply the stain next. Begin at one end and spray or brush the stain on the wood. Slowly and carefully work your way along the grain to reach the opposite end. Make sure that the stain does not drip off the edge of the wood. Before proceeding to the next step, let the stain dry thoroughly.
To protect the painted surface, apply a coat of clear polyurethane sealant. Apply three coats with polyurethane. Allow the third coat to dry overnight before sanding the final coat.